To buy or not to buy – that is the question…
27 May 2022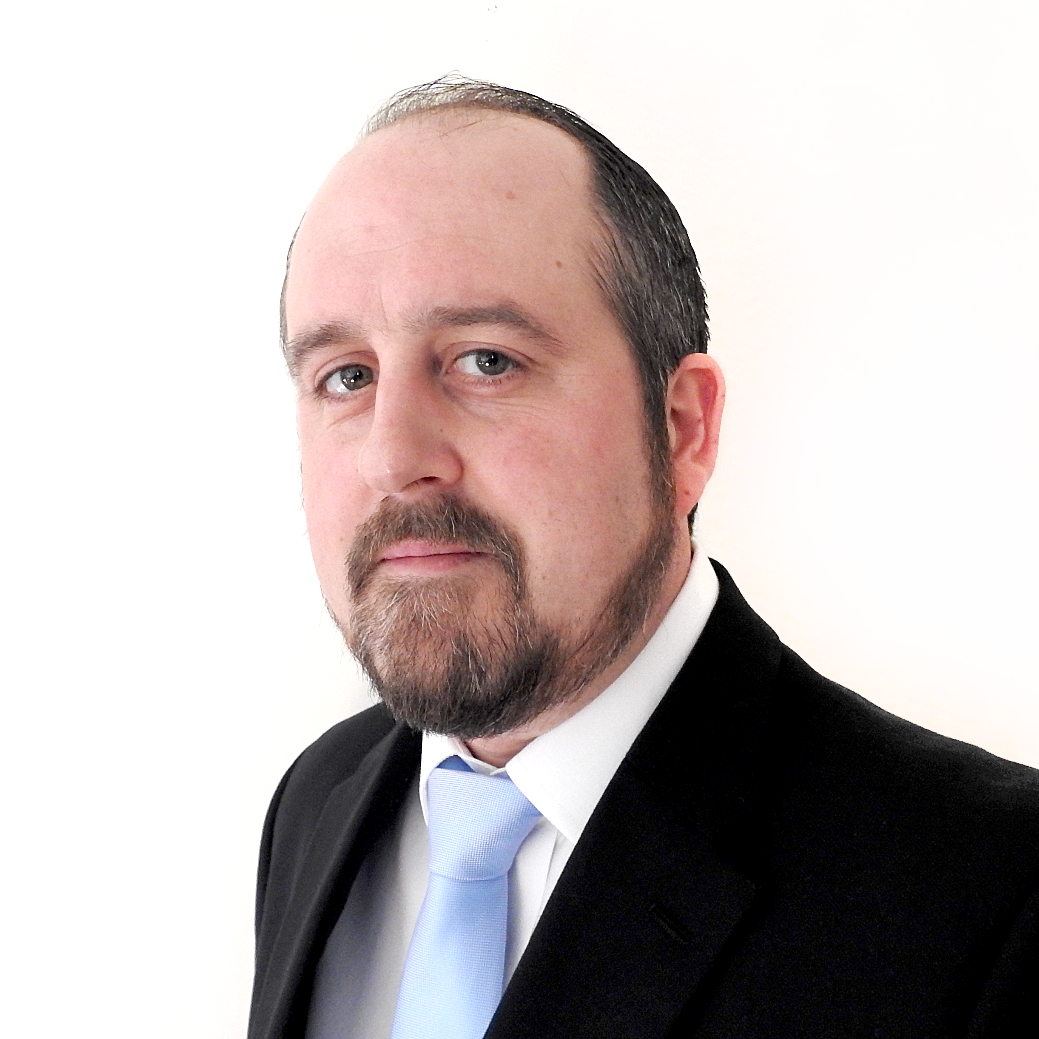
I’m often asked my opinion on whether it is better for food manufacturers to buy or lease production space. As with most things in life, the answer isn’t black and white.
For smaller manufacturers with a small capacity requirement and no complicated manufacturing process, it can be more cost-effective to work with a co-packer or even in the short term to rent space and covert it into a food manufacturing facility, particularly if it is a bespoke food manufacturing process.
However, the savings gained initially on renting/converting space can easily be spent on dilapidation – putting the facility back to how it was at the end of the rental term – which can easily reach into millions of pounds and results in a large amount of equipment with no home.
For larger manufacturers there is a tipping point at which there is greater value in building a bespoke facility and wrapping the building around process rather than the other way round.
While it may seem initially that renting is the cheapest and most time-effective way to set up a food manufacturing facility, by the time you have identified the upgrades the building requires -drainage/effluent treatment/change of use/services etc (all for the landlord’s benefit) you may find that you are left with a large, cladded steel frame in a location that isn’t ideal and costs more to operate than you bargained for.
As an example, we recently conducted a feasibility for a client who wanted to understand the rental/fit-out option (effectively using a spec build to fit-out) for manufacturing. The costs were astronomical, compared with a bespoke build significantly more suited for their needs. This came as a surprise to the client however they have now changed their business plan to bespoke for this size of facility.
Many sites are built with the logistics sector in mind (warehouse space/speculative build). Converting these to food facilities often involves taking things out (concrete floor slabs for drainage etc) and adding items in (steel strengthening) which would all be captured as part of a bespoke build.
Working backwards to design the building around the process enables massive efficiency to be built into the design. In one facility, we were able to separate high care and low care goods into different floors with product ingredients being dropped directly into the required point of the production process. Similarly, siting chemical storage areas directly by the tanks where they will be required separates these hazards from other processes and mitigates risk.
Building efficiencies into the design of the production facility has been shown to result in around 20%+/- lower running costs, both through optimisation of the production process and through savings gained by having a smaller facility with lower energy requirements.
Working with the existing utilities infrastructure also guides the equipment specification process – in one case we were able to save a client a significant annual cost by changing the specified equipment to gas that was readily available rather than the original electrical equipment spec that would have required a significant investment to upgrade the electrical systems to cope with the increased electrical load.
Engaging a specialist food manufacturing project company early in the process to conduct a feasibility study will identify the most appropriate solution for your specific needs, based on your manufacturing processes, future growth plans, locations, availability of utilities and long-term objectives.
At DDK, we won’t tell you to build a factory if you don’t need one – we pride ourselves on always acting in our customers’ best interests. But if you do need one, we will advise you on the very best solution for your requirements that will maximise your return on investment.