Driving best practice in food construction standards
12 October 2022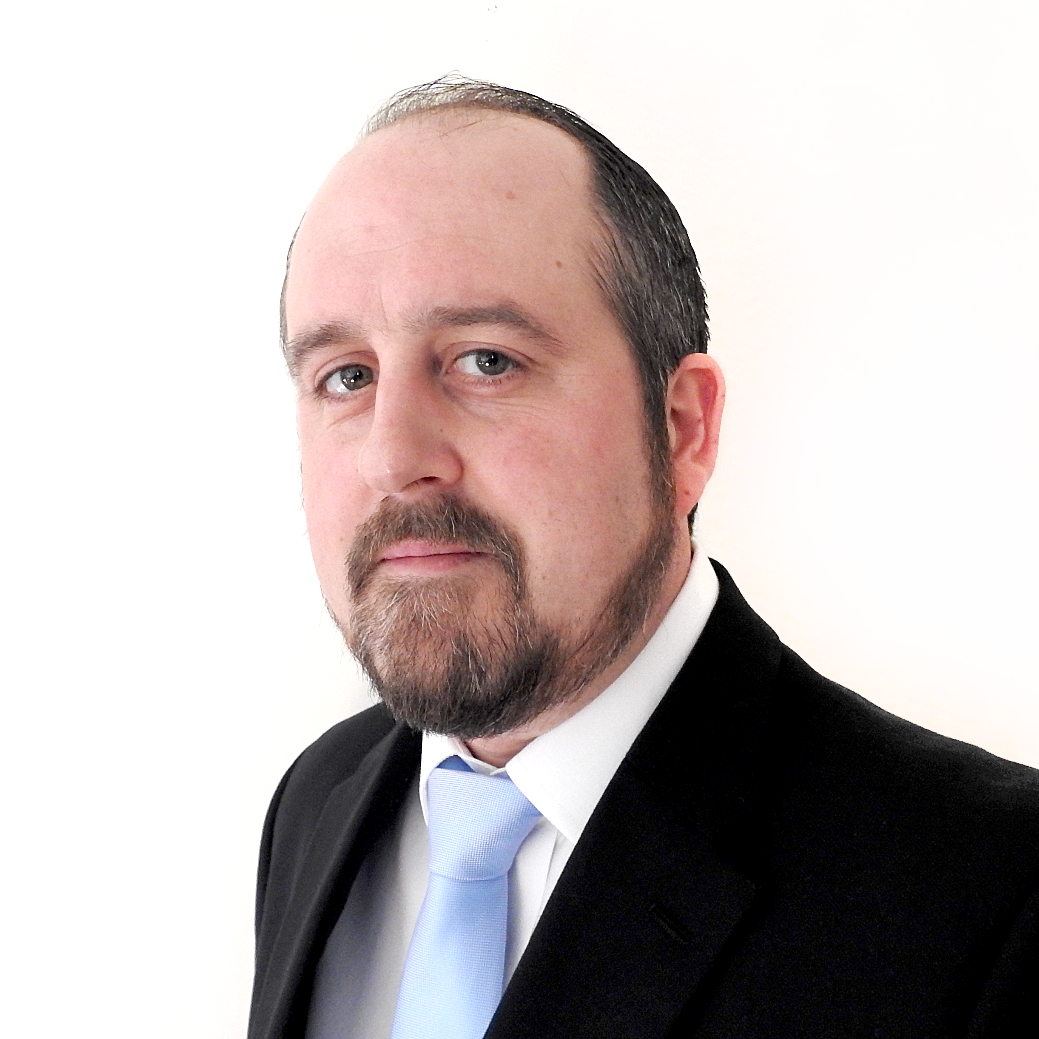
Many food manufacturers do not have standard specifications for their production facilities, and using different design consultants, contractors and suppliers can lead to vastly different quality standards across factories owned by the same organisation.
Creating a standard specifications manual is a worthwhile investment of time to ensure consistency across sites and makes issuing tenders considerably easier.
Here are five top tips to consider when planning a standards manual.
- Technology
What new products are available in the market and what is the latest available technology? Keeping a finger on the pulse of new product development through your supply chain network can enable you to rethink systems and processes to be more efficient and productive.
- Stakeholder engagement
Seek out feedback from different parts of the business to understand exactly what they need in order to maximise performance. Those on the frontlines will know where the pinch points are in their daily processes and are best placed to inform the research process.
- Process integration
Consider all of the different processes that are required in your facility and how they interact with each other and how the operations flow through the building. This is where detailed understanding of technical construction is required to know what can and cannot happen in close proximity.
- Identify supply specifications
Every item that goes into your facility, from floors to doors to sinks to machinery, should have a minimum standard specification. In some cases, you will want to specify actual manufacturers and products to ensure consistency of quality.
- Adapt standards
Outline a set of central core standards and then add on specific standards for different facilities. For example, a cleaning process will be different in a bakery to the same in an abbatoir, however the core principles, products and systems will remain the same.
Employing a specialist consultancy to carry out this process can often be the most cost-effective approach due to their wider knowledge of the industry, available technologies and best practice.
It’s companies like DDK that deliver the construction who fully understand the standards that need to be met. It’s not always what you see but what goes on behind the scenes.