Cost of living crisis impacts on capex projects
18 January 2023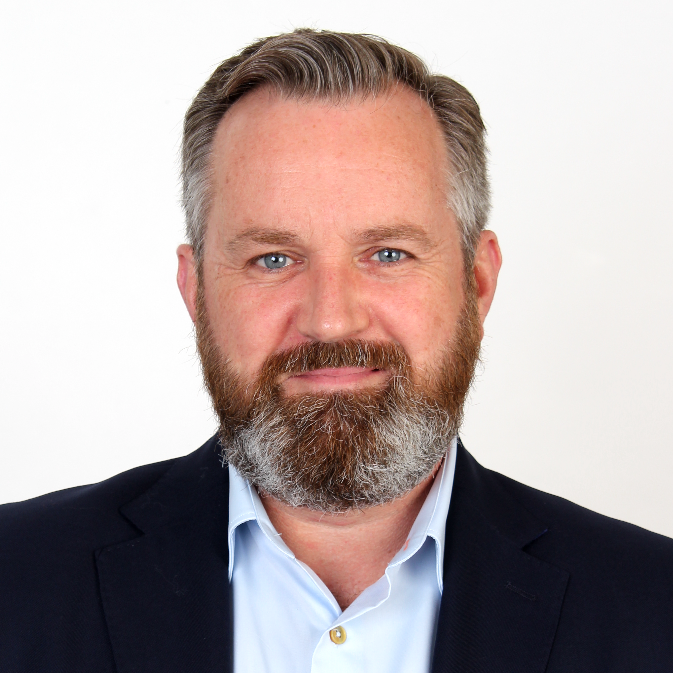
It cannot have escaped most people’s attention that we are in the grip of a cost-of-living crisis that is predicted to go on for some time.
As consumers reduce their spending or switch to cheaper options, manufacturers are seeing their bottom lines under pressure with a need to offset the impact of cost increases in all areas – energy, ingredients, packaging and labour, including investment project costs.
Within many areas to focus on from cash to operating margin, DDK consider three approaches often used in project delivery that can be leveraged to help achieve this.
- Phasing of large-scale investment programs (cash)
Any planned transformational projects such as expansions, new sites or new lines can be phased so that investment cost and access to the returns happens in a structured and prioritised way. For example, a large new facility build can be designed to deliver unit by unit, bringing capacity online in stages that optimise a multi-year cost operating model. This often results in a modular approach where building a large shell allows the fit out and operation of the new footprint to be carried out in stages over time. This approach can be used to deliver staged sustainability objectives and to maximise the impact of energy efficiency opportunities. Significant investments can still be considered, albeit staged over time with a phasing strategy a key part of the project definition.
- Flexible Automation (Manufacturing cost)
Automation has increasingly been on the agenda in recent years due to the lack of available labour to operate traditional production lines. The cost-of-living crisis and associated need to reduce input labour costs has dramatically increase the focus on this area. A cold-eye review of production processes can offer up many opportunities for automation, ideally with flexibility built in so that only minor changes are needed to deliver different product ranges from the same lines.
- Value engineering (Reducing absolute cost)
Value engineering is one of the key parts of a good construction project process where every opportunity is considered. If this is applied across the value chain it would involve looking at all options for simplification and cost reduction – product, packaging and manufacturing processes. It might trigger some interesting ideas if the challenge was “What would we do if were doing this for the first time in a new facility where everything is up for challenge?”.
While individual changes and improvements can initially appear minor, taken in the round the cumulative effect can have a significant impact on profitability.
The businesses that successfully survive the current crisis will be the ones that look for small, incremental changes across the entire business to protect margins while meeting the needs of consumers.
If you would like to discuss any of the above examples, or wider, in this context, please feel free to contact DDK here.