Inside the Critical Path – a new approach
14 March 2023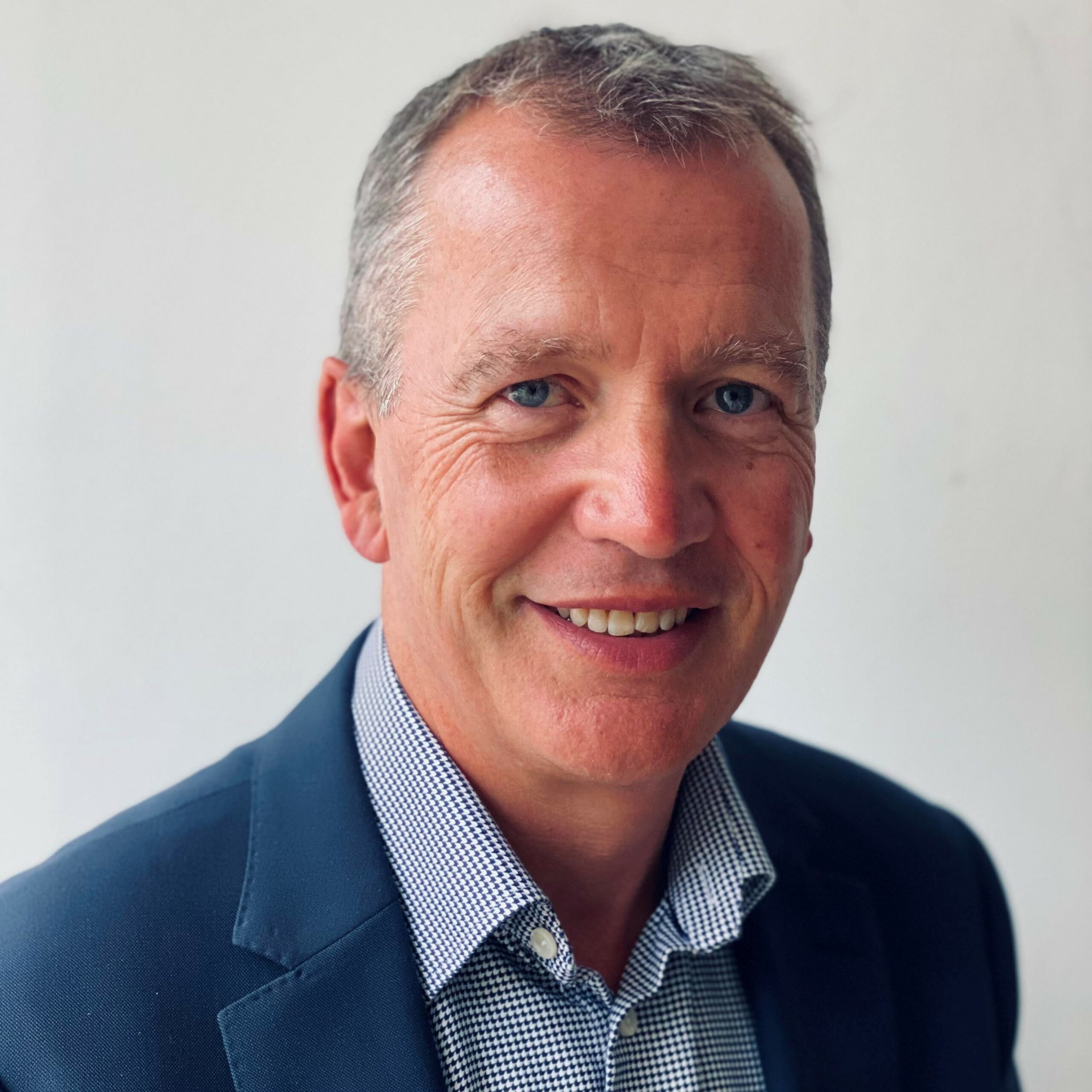
When Samsung decided to enter the Biopharmaceutical sector as a CDMO (Contract Development and Manufacturing Organisation), they established Samsung Biologics and set out to build a Biologics manufacturing facility in half the time that anyone else could do it. The approach they took was on the face of it simple and brilliant: it was to deconstruct each of the project tasks and find ways to do them faster and in doing so dramatically shorten the overall critical path. Of course, it also helped having as their construction partner Samsung C&T’s Engineering and Construction Group, a multi-billion dollar construction company used to undertaking mega projects, including the Petronas Towers, which remains the tallest twin tower building in the world having been the tallest building until 2004.
One of the conventions they managed to stand on its head for a building constructed of concrete, was to redefine the time taken to be able to start casting on the first floor. To do this they had to find a way to accelerate the preparation and installation of load bearing columns. A traditional factory build is necessarily constructed in phases – the groundworks have to be completed before you can start building above ground. The cutting, bending and fixing of rebar and formwork need to be completed before the pouring and curing of columns and slabs can commence. Typically, the roof has to go on before you start work on the internals. In the early part of a typical project these are the activities that drive the schedule and they are often hindered by site constraints that limit the logistics capacity. This was not the case in Incheon, South Korea.
Imagine the morning of t-zero on site in May 2011, with a precisely prepared pile cap already in place; everything was ready to go to start the installation of a forest of ground floor columns*1 that had been prepared offsite and were waiting to be lifted into place, before the concrete pouring could commence; (note*1 in this case the bending schedule included embedded steel plate that removed the need for column formwork and enhancing their initial load bearing capacity). Contractor capability matters, so with more than 70 ready-mix trucks and 4 concrete pumps on standby and a convention beating plan Samsung Biologics were ready to challenge industry benchmarks and expectations.
The impact of fixing the columns to the pile cap was that in a matter of weeks work was underway installing the first-floor slab. With this level of precise planning and enormous resources the building structure was already well on its way to early completion. The deconstruction and challenging of assumptions that make up an established project task wasn’t limited to the building construction; it was applied to every other aspect of the project as well. The detailed lead times used by OEMs for their equipment manufacture were subject to detailed review and challenge. Where there was opportunity Samsung Biologics stepped in to interfere with the default assumptions thereby recalibrating promised lead times; for example they knocked weeks off the lead time for stainless steel 316 tube supply that was on the critical path for one OEM, which enabled a like for like improvement in the equipment delivery.
Every opportunity was explored including de-prioritising the offices to get to beneficial use as early as possible. An innovative Master Validation Strategy was deeply integrated into the project, and this enabled significant reductions to the normal time associated with validation tasks. An example of this was the pre-qualification, testing and training done on the automated bioreactor systems prior to their early installation, which required careful shrink wrapping and protection to prevent dirt ingress and damage but allowed months of critical path time to be saved. What was the result? The facility was built and ready to operate in half the time typical of similar sized projects in the sector.
The point is this: the assumptions on which a building schedule is based relate to the method of construction, equipment capability and the past experiences of the project team. If everything is stick-built on site, then the resulting critical path will always be driven by a series of sequential activities with significant interdependencies. Progress is made by constantly challenging and questioning why something is the way it is. Using an approach that incorporates modular and off-site construction provides the opportunity to decouple activities and eliminate interdependencies and reduce onsite construction time. As a result of this trend, we are gradually moving construction towards increasingly manufactured solutions.
At DDK our Construction Management System (CMS) will create a schedule and predict a critical path for a project. The CMS was put together by deconstructing each task in a typical build and putting it back together in a systematised approach that orders and sequences the activities, all based on the current expected durations from our supply chain partners. It doesn’t stop there, we use the schedule to identify and, if possible, design out problems and constraints. It is also updated when real world factors cause changes. The CMS allows DDK to master the complexity of a build and provide a level of planning detail to clients that creates confidence in effective project delivery.