What do you learn when you try to put a Factory in a Box?
10 May 2023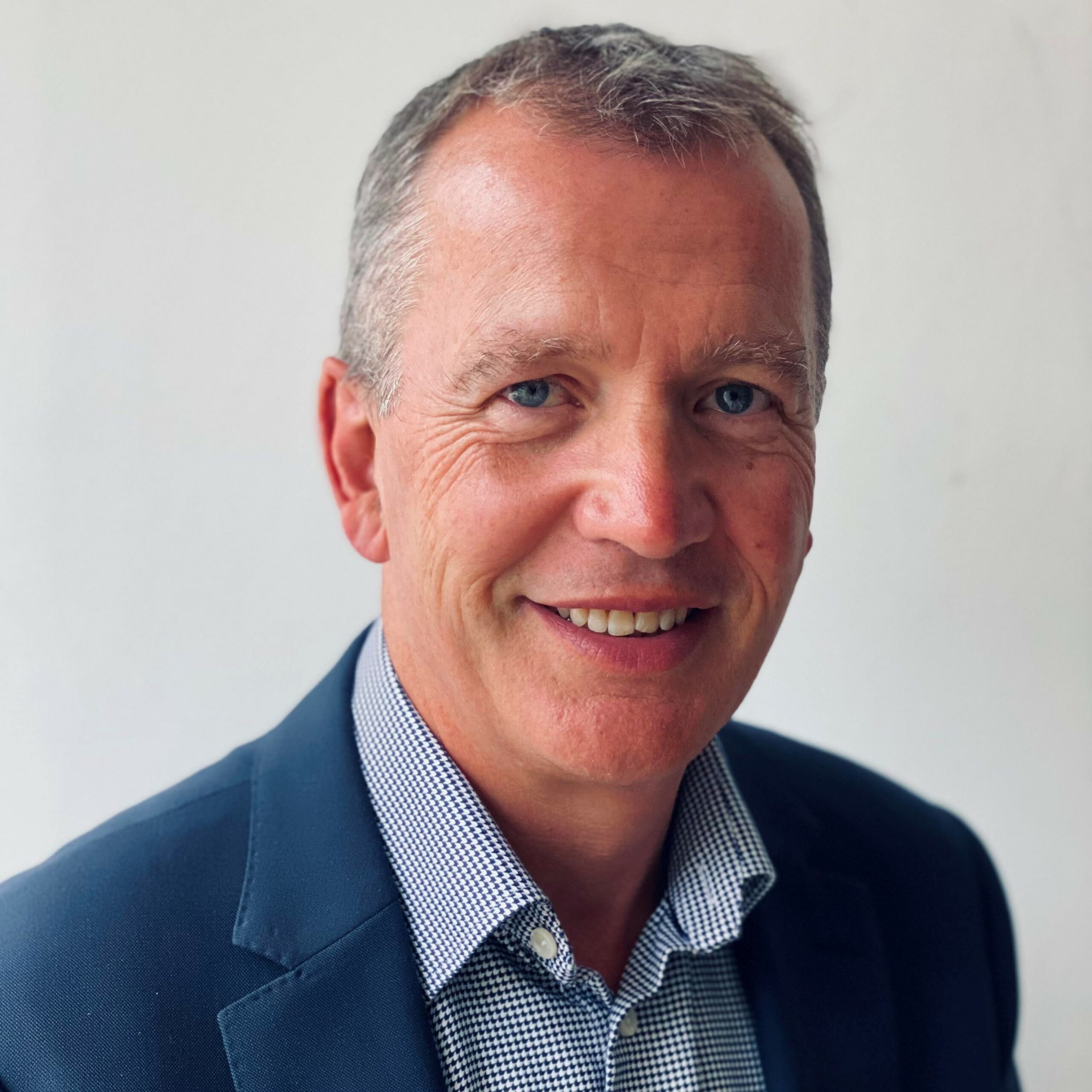
If you want an accelerated learning experience, simply try doing something completely new. We were interested in how we could guarantee the final delivered quality of a highly regulated facility by stretching the work done on the supply-side as much as we could. This is what we learned when we tried to put a factory in a box.
Can you build a factory from a flat pack kit?
The short answer is yes (!) – but doing so forces different approaches to be adopted by both the supply and delivery teams. Detailed kit-thinking demands that each part is identifiable and its final (and possible) position(s) in the structure is/are defined. To manage this complexity, it becomes necessary to (2D bar code) label each individual component and provide colour coded location and centreline markers on the structural steel for ductwork and services. Finally, the digitised instruction manual requires the equivalent of a Poka Yoke exercise on the entire assembly library to make sure it is fit for purpose.
So is this level of new and additional effort worth it?
Once everyone had figured out how to use their iPad (the digitised instruction manual), you saw and could measure the impact on productivity that the accurate design tags, prefabricated parts and a corresponding step by step approach had on the site assembly operation. This was all with the ultimate purpose to deliver a final build quality as good as you would find in an equivalent facility in Europe or the USA built using a conventional approach.
The Beta Build
The beta-build project, in this case of a mini-pharmaceuticals factory, was completed to test and establish how difficult it would be to pre-fabricate and containerise a factory, so that it could be re-assembled with minimal construction equipment, basic oversight and requiring only that the concrete base be precast at the final location.
The quality target was for the internal finishes, HVAC system performance and the entry and exit routes for materials and personnel to meet or exceed the highest regulatory standards. If you like, the purpose of this challenge was to create a highly regulated factory that could be packed and shipped anywhere.
One of the problems the design team needed to address was the work that would be done at height in a standard construction project. This was achieved by completing the roof service space assembly at ground level before raising it to the final ceiling level. (See photo below)
The final results were staggering; with on-site productivity measured at 85%, which compares to an average construction site productivity of 30%. Virtually zero waste and the assessment of the build quality was that it met its target.
Validation
It’s funny how these things happen. In the summer of 2015, just after we had finished the Beta Build, I was travelling back to the UK from China and happened to notice the passenger next to me was doing some engineering sketches. I asked where he had been in China and he replied that he had been visiting the company responsible for the Birds Nest Stadium. We chatted and he explained that the company were fabricating fully- finished modules that could be effectively push fitted together on site. In a similar way that student university accommodation blocks can be erected in only a matter of weeks or cruise liner cabins are installed. He explained that by doing all the hard work in the factory they had effectively eliminated on-site waste! He then asked me to guess what the fabrication tolerance was that they used. I nearly choked when he said 0.1mm.
So what’s the point of all this?
Being able to incorporate offsite modular construction or kits based on standard proven designs into a project has clear advantages, whether it is a prefabricated service skid, standard changing room kits or proven service walkway layouts that facilitate installation, in-use maintenance and expansion. These approaches deliver multiple benefits by making the on-site construction quicker, more cost-effective, with less waste and deliver a guaranteed end quality.
At DDK we know this and have developed a number of proprietary design elements for use within potential factory layouts. Our philosophy is to develop client specific solutions that are repeatable, reusable and scalable. Get in touch if you would like to know more about our modular build solutions.