Eight reasons why capex projects go wrong
25 October 2022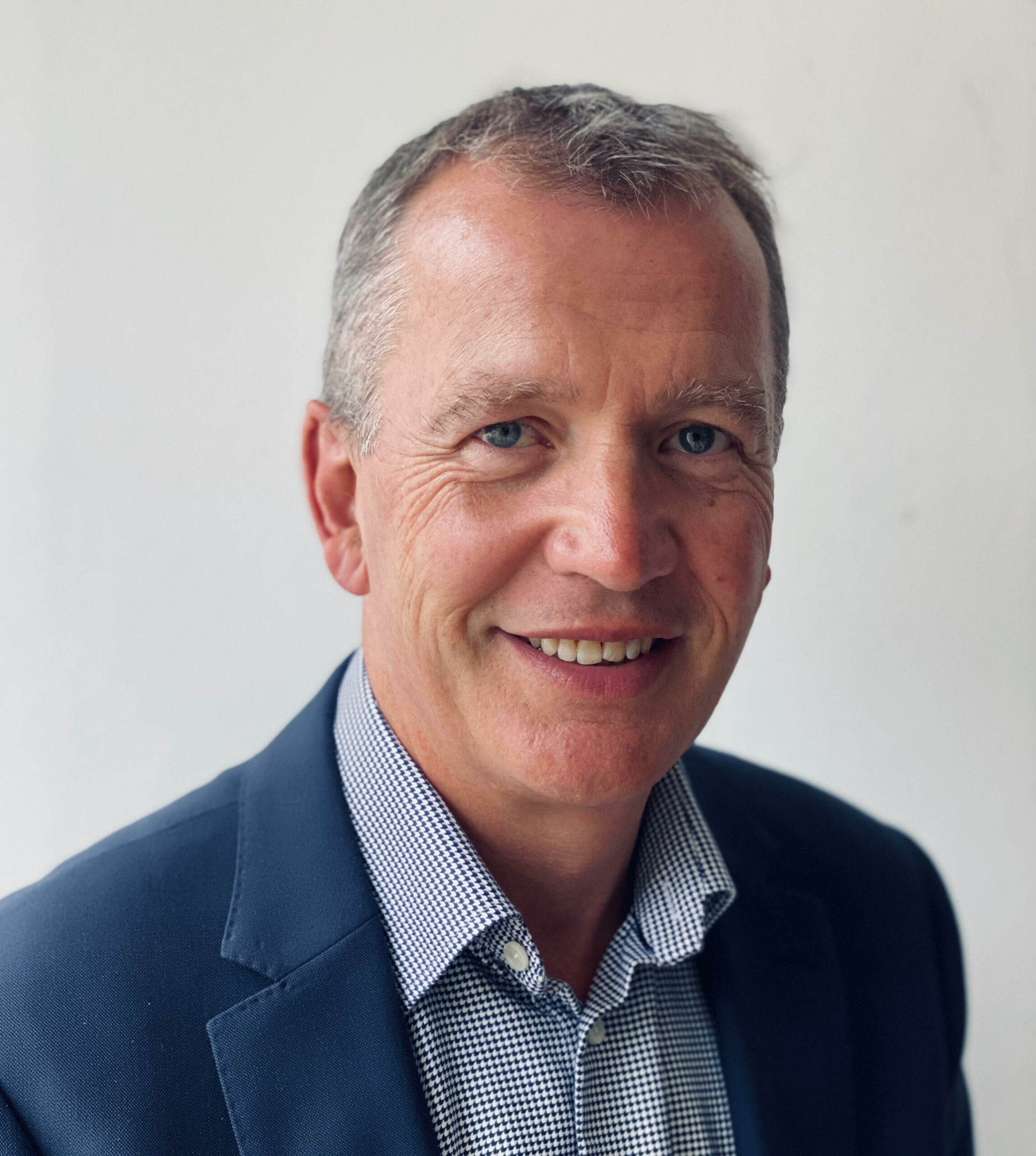
- Fundamental errors
One error that is surprisingly common is building unnecessarily. Ask yourself a few fundamental questions: Is this the right project? Do you actually need this project? Are you building the right size and capacity or is it too big? Is it based on solid market fundamentals?
One approach is to test the idea and try to kill it off – if it still stands up to scrutiny under different scenarios then you are on the right track. DDK’s philosophy is that less is always better – build the smallest footprint possible to achieve your objectives.
- Not understanding the strategic term
The strategic term is the expected life, in years, of the product or category in which an investment is being made. Ideally the project payback period is significantly less than the strategic term and should be a strong factor in project portfolio prioritisation. The strategic term should be agreed by the Board and built into financial forecasting as part of a robust business case. Alternative strategies such as third party manufacture should be considered if the strategic term is too short or uncertain.
- Duplication of work
Don’t re-invent the wheel as the saying goes. Applying modular strategies and designing “cookie-cutter modules” that can be easily replicated, as and when required, allows for a controlled and efficient build.
- Not applying segmentation strategies
Smart segmentation strategies can reduce or eliminate opportunities for contamination and are essential. For example, for allergen control. This thinking applies equally when segmenting ventilation systems or controls systems to reduce the risks from cyber attack. In the case of ventilation, segmenting similar processes together enables you to standardise air change rates and ventilation according to the risk factors present.
- Lack of quality control
Project quality control is vital during the specification process. It is essential to choose something that can actually do the job you are asking of it, whether that is machinery, equipment or infrastructure. The Project Engineering and Procurement teams need to work closely together in order to ensure that every item purchased is fit for purpose. You could also consider developing a standards specification manual for all capex projects. Here are our tips for where to start: Driving best practice in food construction standards – DDK (ddk-ltd.com)
- Transactional errors
A project is made up of hundreds of thousands (if not millions) of transactions, many of which are interdependent. A comprehensive project management system is essential to keep track of the various workstreams and critical paths where pitfalls can occur.
- Calculation errors
This can be human error in measurement, calculation or simply incorrect data entry that can lead, for example, to significant over or under ordering of material. Automated cross-referencing of calculations should bring most of these mistakes to light before they happen.
- Cumulative errors
What can begin as very minor errors can quickly grow in magnitude when spread across the scale of a major project if left unchecked. Regular stage-gate or steering reviews should be common practice that help keep projects on track.
DDK’s Integrated Project Delivery (IPD) model ensures that all factors, and more, are considered during the Define phase of planning to make sure that the whole team on both client and contractor sides is Project Delivery Ready. Get in touch through our contact form if you would like to know more.